Xiangsheng
Customized carbon fiber components
Customized carbon fiber components
无法加载取货服务可用情况
Introduction to the production of carbon fiber special-shaped accessories:
1. Design and planning:
- Demand analysis: Have full communication with customers to understand the specific usage scenarios, performance requirements, dimensional accuracy and other needs of special-shaped accessories, and clarify the production goals and directions.
- 3D design: Based on the results of demand analysis, use professional 3D design software to design the detailed model of special-shaped accessories. In the design process, factors such as the characteristics of carbon fiber materials, the limitations of processing technology, and subsequent assembly requirements should be considered to ensure the feasibility and rationality of the design scheme.
- Scheme optimization: Evaluate and optimize the preliminary design scheme, including aspects such as the rationality of the structure, mechanical property analysis, and the difficulty of the production process. Through optimized design, improve the performance and production efficiency of special-shaped accessories and reduce production costs.
2. Mold making:
- Mold design: According to the 3D design model of special-shaped accessories, design the corresponding mold. The design of the mold should consider factors such as the shape, size, accuracy requirements, and demolding method of the accessories to ensure that the mold can meet production needs.
- Mold material selection: The selection of mold materials should be comprehensively considered based on factors such as production batch, complexity of accessories, and cost. Commonly used mold materials include steel, aluminum alloy, composite materials, etc. Steel molds have the advantages of high strength, good wear resistance, and high dimensional accuracy, and are suitable for mass production; aluminum alloy molds are lightweight, easy to process, and have low cost, and are suitable for small batch production or trial production; composite material molds have good thermal insulation and corrosion resistance properties and are suitable for the production of some special-shaped accessories with special requirements.
- Mold processing: According to the mold design drawings, use mechanical processing, electrical discharge machining, numerical control processing and other methods to make each part of the mold. During the processing process, the dimensional accuracy and surface quality of the mold should be strictly controlled to ensure the quality and service life of the mold.
- Mold assembly and debugging: Assemble the processed mold parts and conduct debugging and inspection. During the debugging process, check whether the opening and closing movement of the mold is smooth, whether the fit between each part is tight, and whether the dimensional accuracy of the mold meets the requirements. For some complex molds, trial molding is also required, and the mold is further adjusted and optimized according to the trial molding results.
3. Raw material preparation:
- Carbon fiber selection: According to the performance requirements and usage environment of special-shaped accessories, select the appropriate carbon fiber material. Factors such as the type, specification, and performance indicators of carbon fiber will affect the quality and performance of special-shaped accessories. Common carbon fibers include polyacrylonitrile-based carbon fiber, pitch-based carbon fiber, etc. Among them, polyacrylonitrile-based carbon fiber has the advantages of high strength, high modulus, and high temperature resistance, and is currently the most widely used carbon fiber material.
- Prepreg preparation: Mix the selected carbon fiber and resin matrix in a certain proportion to prepare prepreg. Prepreg is an intermediate material for the production of carbon fiber special-shaped accessories, and its quality directly affects the performance and quality of special-shaped accessories. In the preparation process of prepreg, parameters such as the proportion of carbon fiber to resin matrix, mixing uniformity, and resin content should be strictly controlled to ensure the stable quality of prepreg.
4. Molding process:
- Layup: Lay the prepared prepreg on the mold according to the designed layup angle and sequence. During the layup process, pay attention to the flatness, adhesion, and fiber direction of the prepreg to ensure the mechanical properties and dimensional accuracy of special-shaped accessories.
- Curing: Put the laid prepreg and mold into the curing equipment and, under certain temperature, pressure, and time conditions, cure the resin matrix to form a blank of carbon fiber special-shaped accessories. The curing process is a key link in the production of carbon fiber special-shaped accessories. The control of curing temperature, pressure, and time should be strictly adjusted and optimized according to the performance of prepreg and the requirements of special-shaped accessories.
- Demolding: After curing is completed, take the mold out of the curing equipment. After the blank of special-shaped accessories cools to room temperature, perform demolding operations. During the demolding process, pay attention to avoiding damage to special-shaped accessories to ensure the surface quality and dimensional accuracy of special-shaped accessories.
5. Post-processing:
- Machining: Machine the demolded blank of special-shaped accessories to remove excess materials and improve the dimensional accuracy and surface quality of special-shaped accessories. In the machining process, select appropriate cutting tools, cutting parameters, and processing technologies to avoid damage to carbon fiber special-shaped accessories.
- Surface treatment: According to the use requirements of special-shaped accessories, perform surface treatment such as painting, coating, anodizing, etc., to improve the corrosion resistance, wear resistance, and aesthetics of special-shaped accessories.
6. Quality inspection:
- Appearance inspection: Inspect the appearance of carbon fiber special-shaped accessories to check whether there are defects, scratches, bubbles and other problems on the surface to ensure that the surface quality of special-shaped accessories meets the requirements.
- Dimensional accuracy inspection: Use measuring tools, coordinate measuring machines and other equipment to inspect the dimensional accuracy of special-shaped accessories to ensure that their dimensions meet the design requirements.
- Mechanical property inspection: Inspect the mechanical properties of carbon fiber special-shaped accessories, such as tensile strength, bending strength, shear strength, etc., to ensure that their mechanical properties meet the use requirements.
7. Packaging and transportation:
- Packaging: Package the inspected carbon fiber special-shaped accessories and use appropriate packaging materials and packaging methods to ensure that special-shaped accessories are not damaged during transportation.
- Transportation: Select the appropriate transportation method and transportation tool to transport the packaged carbon fiber special-shaped accessories to the location designated by the customer. During the transportation process, pay attention to avoiding problems such as collision, extrusion, and moisture of special-shaped accessories.
Share
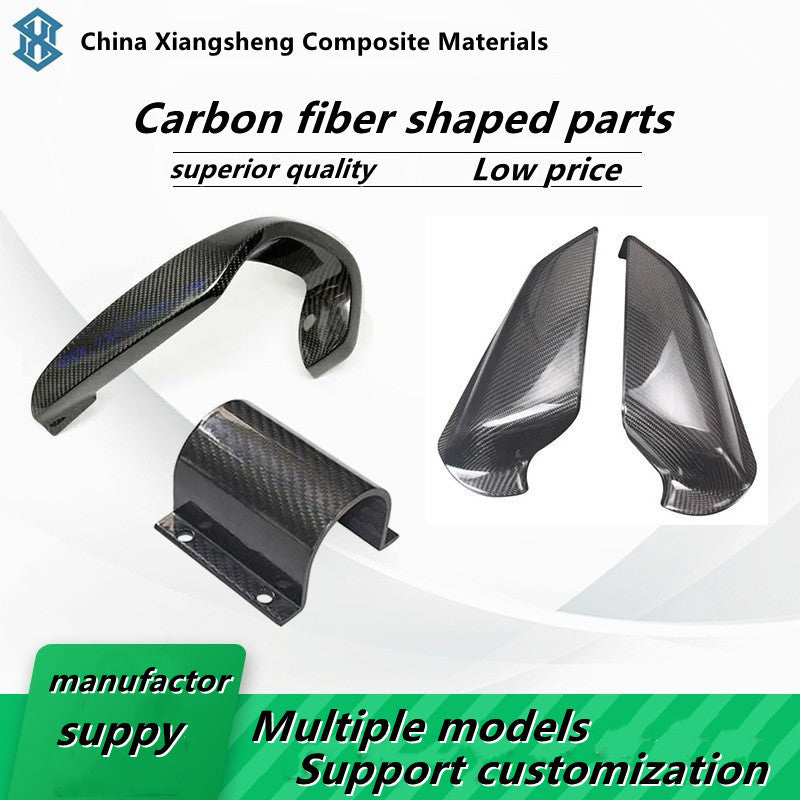
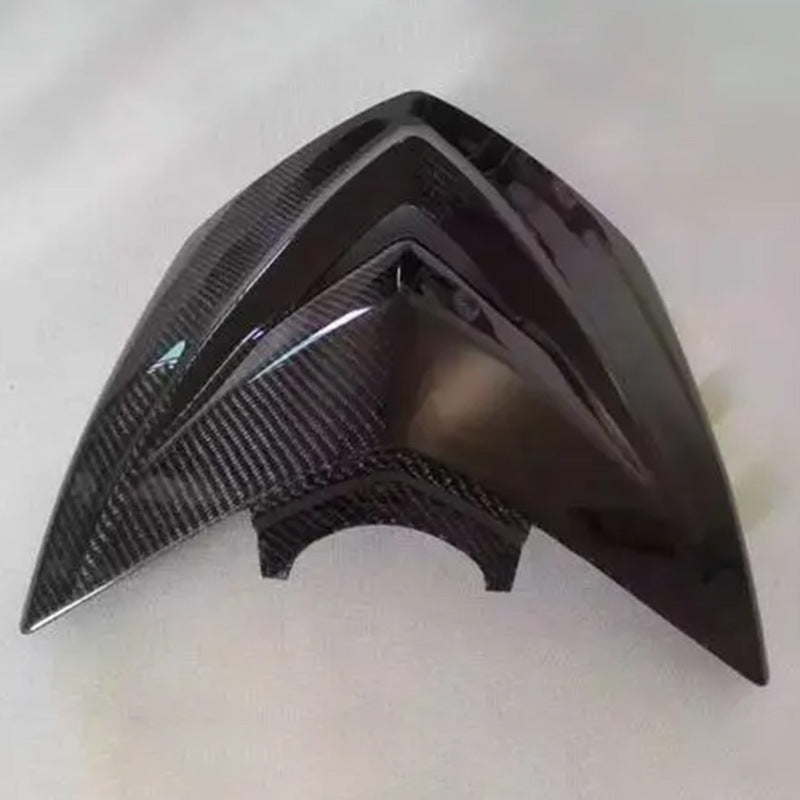
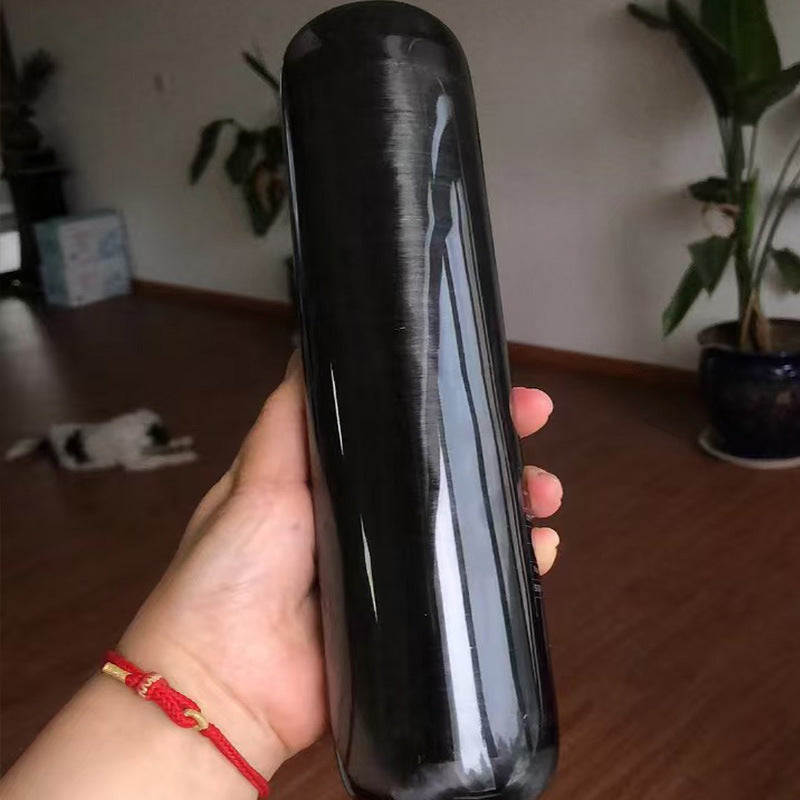
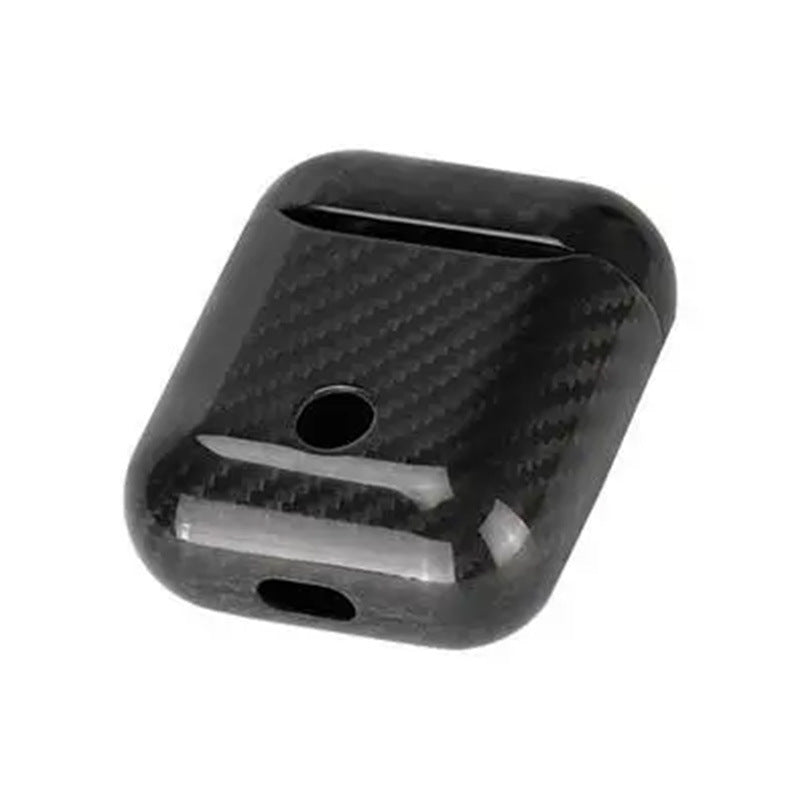
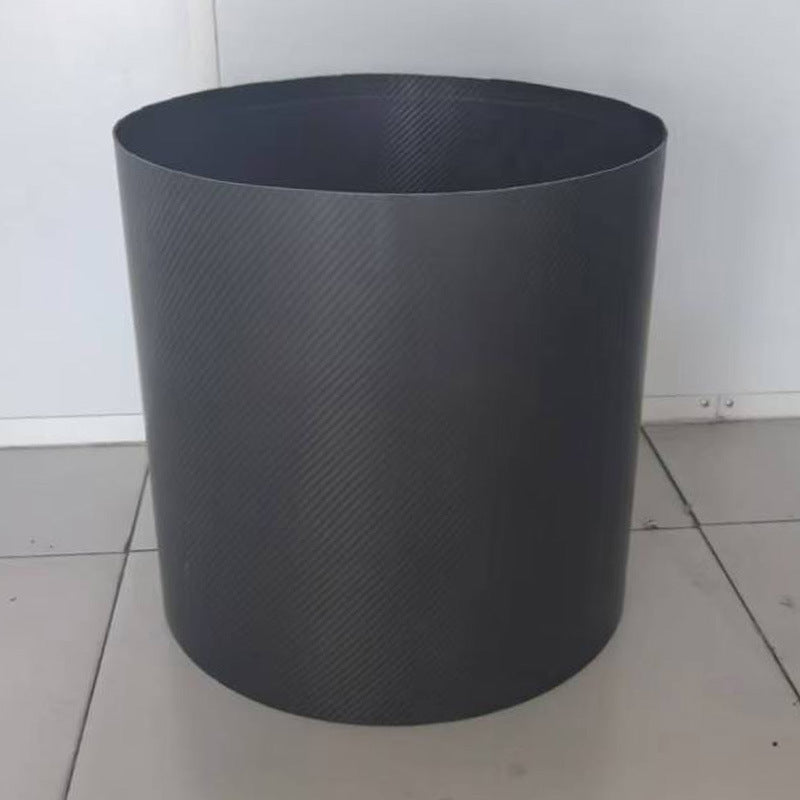
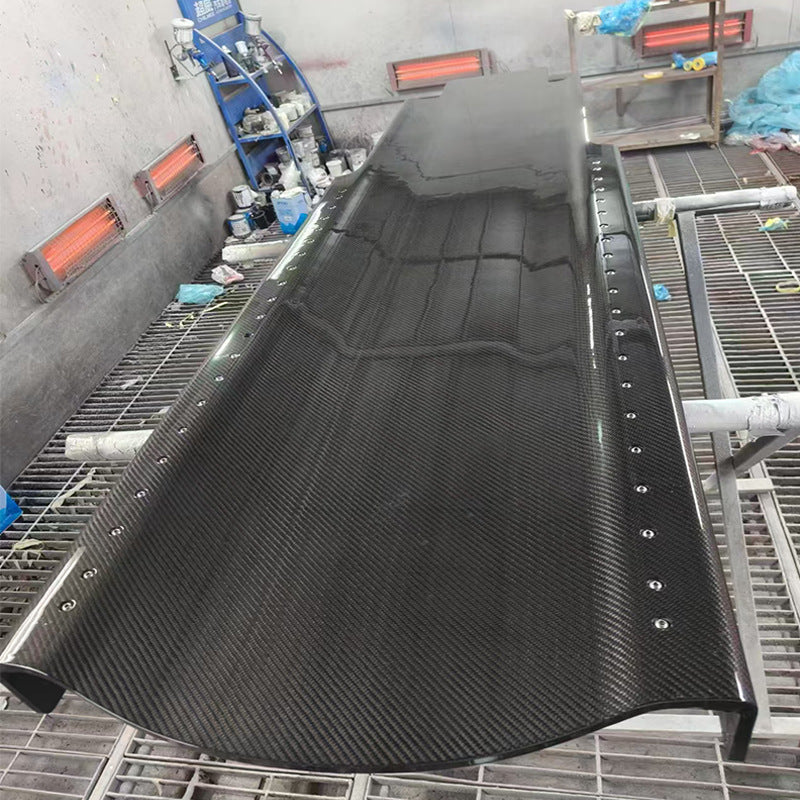